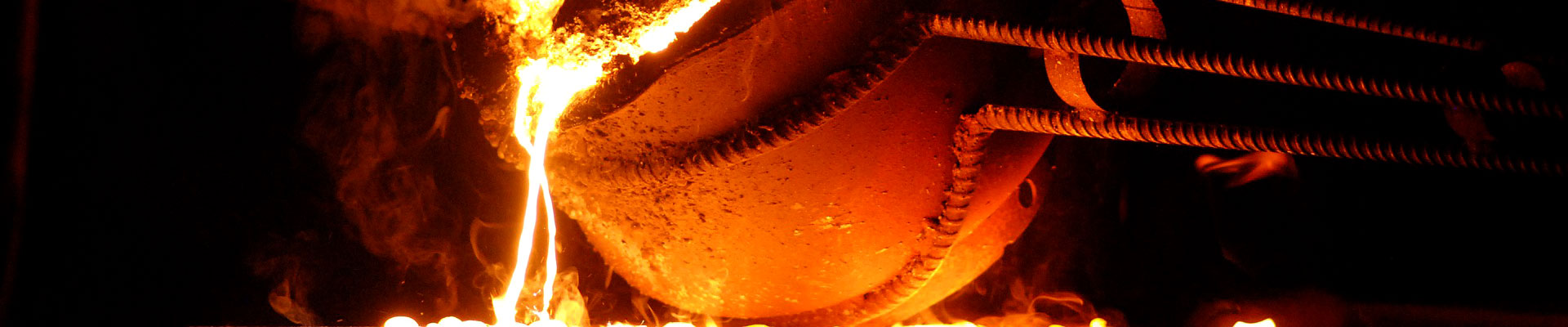
Frequently Asked Questions
We can work with to gather the information we need by phone or email. If possible, we request you provide us with the following information:
- A 2D and/or 3D drawing
- Material specification including heat treatment
- Quality assurance expectations
- Special finishing requirements
- Tooling if required or existing
- Due date of quote response
After receiving your request to quote, CFI analyzes the information to determine:
- Tooling requirements – best suited to scope of your project
- Quality expectations required to support your technical specifications
- Machining requirements are reviewed and understood
- Finishing requirements are reviewed
- A realistic delivery date is determined
- Based on this review, we make recommendations for the project and provide you with a quote
Each alloy serves a difference purpose based on issues as diverse as heat exposure, run time, weight requirements, flexibility of the end product and so on. We work with you to determine exactly how your component will need to perform and then guide you to the best alloy whether you need:
Ferrous Metals | Nonferrous Metals |
---|---|
Cast Iron | Cast Aluminum |
Gray Iron | Cast Copper Alloy |
Ductile Iron | Brass |
Malleable Iron | Bronze |
Compacted Graphite Iron | Zinc |
Cast Steel | Magnesium |
Carbon & Low Alloy | Titanium |
Corrosion Resistant | Nickel |
Heat Resistant | Cobalt |
Manganese | Tin |
Casting is one of the fastest and most cost-effective methods for producing a wide range of components. However, to achieve maximum benefits, you’ll want to involve CFI at an early stage of the product design and development. We have the expertise and experience to consult with you during the design phase so our engineers can help resolve issues affecting tooling and production methods, while identifying the various trade-offs that could affect overall costs.
We have arranged with casting partners to offer the different casting types. Part of the placement process for your project will be the selection of the casting process that will best serve your needs. The most popular form is sand casting which involves making a replica of a finished piece (or pattern) that is compressed with sand and binder additives to shape the final part. The pattern is removed after the mold or impression has been formed, and the metal is introduced through a runner system to fill the cavity. The sand and the metal are separated and the casting cleaned and finished for shipment to the customer.
The basic die casting process consists of injecting molten metal under high pressure into a steel mold called a die. Die casting machines are typically rated in clamping tons equal to the amount of pressure they can exert on the die. Machine sizes range from a few hundred tons to thousands of tons, depending on which cast house partner we assign to your project. Obviously, larger castings are scheduled with large press cast houses while smaller castings can be run on smaller presses. But no matter what size casting you require, the process remains the same.