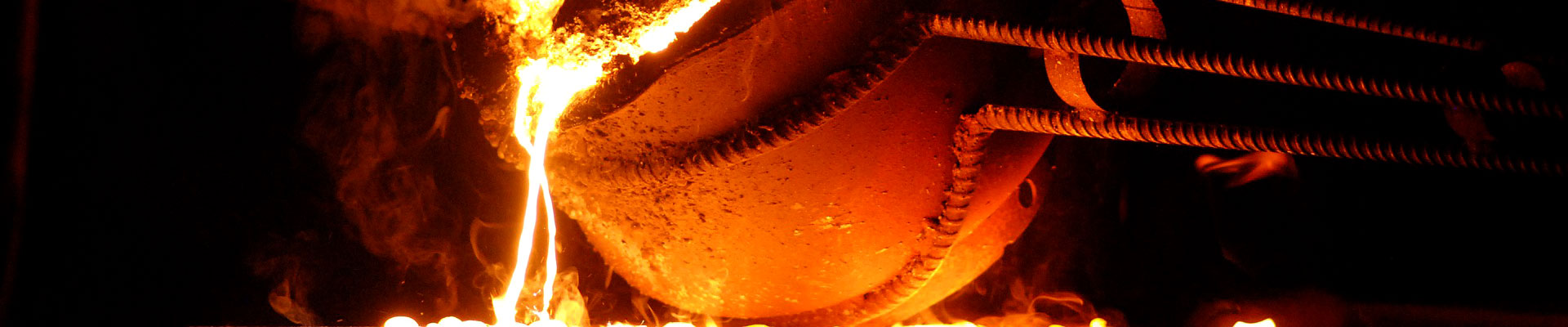
Permanent Mold Casting
The foundry term “permanent mold casting” is used to describe a mold that can be used repeatedly. In contrast to a sand mold which must be destroyed to remove the casting, the permanent mold is designed so that it can be separated to eject and remove the solidified casting. In the current practice, the molds are usually made of cast iron or steel. Permanent mold castings can be produced from all of the metals including iron and copper alloys, but are usually light metals such as zinc-base, magnesium, and aluminum which is by far the most common alloy.
Advantages
The Permanent Mold process produces a sound dense casting with superior mechanical properties. Since the mold is made of metal and is relatively stable, the castings produced are quite uniform in shape and often have higher a degree of dimensional accuracy than castings produced in sand, which reduces or eliminates some of the machining that might be required on the part. The permanent mold process is also capable of producing a consistent quality of finish on the castings. The process also lends itself very well to the use of expendable cores and makes possible the production of parts that for one reason or another are not suitable for pressure die casting process.
Disadvantages
The cost of tooling is usually higher than for sand castings. The process is generally limited to the production of somewhat small casings of simple exterior design.
Precision Molding
Permanent Mold Casting
Typical dimensional tolerances, inches | ± .010″, ± .050″ |
Relative cost in quantity | Low |
Relative cost for small number | High |
Permissible weight of casting | 100 lbs. |
Thinnest section castable, inches | 1/8″ |
Relative surface finish | Good |
Relative ease of casting complex design | Fair |
Relative ease of changing design in production | Poor |
Range of alloys that can be cast | Aluminum and copper base preferable |
Parting Line Influence
When Parting lines are considered, very close tolerances are difficult to obtain. A parting line absorbs fractions of inches per inch. A foundry is doing well to hold a parting line to 0.015 inch. Additional measurement is added to the casting tolerance.