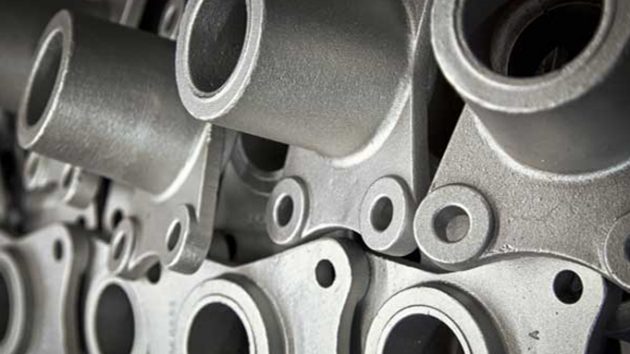
Quality metal casting requires choosing the right pattern equipment for your component. You have many choices in pattern types so it’s best to consult with your foundry before having patterns made. Here are some general guidelines for making this selection:
Prototypes: Inexpensive, possibly loose-molded wood patterns.
Low Volume or Small Batch Runs: Hardwood patterns mounted on boards.
Medium-volume production: Plastic pattern equipment. Shrink-free plastic is ideal for reproducing wood patterns if the wood is still in good shape. Plastic patterns work well when parts will experience a reasonable amount of wear.
High-volume production and shell molding: Metal patterns produced in cast iron or aluminum according to the foundry or process used. Brass or bronze patterns may also be used.
Single impression and machined from solid: Lost wax (investment) castings. Discuss the use of master patterns (replicas of the casting to be produced) with your foundry. Master patterns may be used to facilitate the manufacture of lost wax dies when appropriate.
Complex metal patterns: May be machined from the solid stock or may be cast to shape and then finished to the final dimensions. These are generally very complex involving moving cores and other special capabilities that require a high degree of skill in both the design and manufacture required.
High dimensional accuracy for tight tolerances: Shell cores and shell core boxes may be used for producing cores for castings made from wooden patterns. However, shell cores are normally used with sand-or shell-molded castings where metal patterns are in use.
Your metal caster has experience working with pattern makers and can guide you in choosing the best pattern maker for your application. This decision becomes increasingly important for projects involving complex molds requiring high dimensional accuracy and special capabilities.
Contact us to help with choosing the right pattern equipment for you.
Recent Comments